Aseptic Filling: Key to Net-Zero Food Production
![]() | Progressing Towards Net Zero With Aseptic Filling Technology |
![]() | Tan Hiep Phat Gives Gifts to Disadvantaged Children in Binh Duong on Mid-Autumn Festival |
The Race Towards Net Zero: A Challenging Yet Attainable Goal
The Food and Beverage (F&B) industry is one of the largest sectors, intimately connected to the lives of billion people worldwide. A study by ESG EcoVadis indicates that more than 46,000 F&B companies have an average score of 48.9, placing them among the top three sectors with the highest scores regarding environmental issues and overall sustainability. In recent years, the trend towards sustainable development within the industry has continuously updated, encompassing aspects such as food safety, sustainable sourcing of organic materials, waste recycling, and measures to reduce plastic usage and packaging.
Recently, during the seminar titled "Towards Net Zero: Strategies and Solutions for Reducing Greenhouse Gas Emissions in Food Industry," held as part of the Vietfood & Beverage - Propack Vietnam 2024 exhibition, various practical solutions and experiences were presented by businesses in the food and beverage sector. As demands for Net Zero and sustainability standards increase, particularly in leading global markets such as the US, EU, and China, the trend of prioritizing organic and environmentally friendly products has gained momentum.
![]() |
CEO of GEA Vietnam Vincent Mauer shared insights at the seminar. |
During the seminar, experts provided detailed information and feasible step on maintaining production efficiency while reducing emissions for businesses. GEA, one of the world's largest suppliers of processing technology systems, including machinery, processing plants, and filling equipment for the food, beverage, and pharmaceutical industries, discussed solutions for emission reduction, with a focus on aseptic filling technology. This technology plays a strategic role in contributing to GEA's sustainable development goals and achieving Net Zero by 2040, providing sustainable solutions for many of GEA's partners worldwide, including Vietnam.
The GEA representative outlined specific solutions, including reducing Scope 3 greenhouse gas emissions by 27.5% by 2030, ensuring that 100% of proposed solutions are free from fresh water resources by 2030, and transitioning to sustainable packaging materials for 100% of packaging solutions by 2030. Furthermore, by 2026, all materials used for packaging machinery or spare parts will comply with one of the five R's of the circular economy (Reduce, Reuse, Repair, Remanufacture, Recycle).
Aseptic filling technology, an essential component of any beverage production process, is currently being utilized to minimize environmental impacts.
Aseptic technology encompasses a complex series of interconnected steps, from processing, blending, and sterilizing Ultra High Temperature (UHT) products, to filling and capping to produce a final product. This process occurs within a closed and sterile system, where both the bottles and caps must also be sterilized. Aseptic filling systems are capable of reclaiming sterilizing solutions for bottles and caps (Peracetic Acid - PAA) and reclaiming sterile water, all while maintaining low energy consumption.
According to the CEO of GEA Vietnam, aseptic filling solutions offer numerous benefits on the journey to realizing the Net Zero target. The new sterile water washing system in the GEA ECOSpin has received the GEA Add Better label, significantly reducing water consumption by up to 91% compared to previous versions. Additionally, this system can be integrated to upgrade older equipment, achieving water savings of up to 83%.
Through this aseptic filling technology, the UHT sterilization system utilizes heat exchange technology with lower environmental impact, achieving energy savings of up to 90%, compared to 60% for hot filling.
![]() |
GEA will continue to accompany Tan Hiep Phat in the project of converting the circular economy model, towards the goal of Net Zero. |
Additionally, aseptic technology contributes to minimizing plastic usage compared to other methods, such as hot filling. With GEA's collaboration, each bottled product from Tan Hiep Phat has reduced the weight of the bottle by 50%, now weighing only 13.5 grams. This reduction translates to a 20% decrease in CO2 greenhouse gas emissions for each bottle produced.
Tan Hiep Phat’s Efforts towards Net Zero through Cooperation with GEA
Since developing aseptic technology in 1993, GEA has continually improved it, reaching its seventh generation today. In Vietnam, GEA has partnered with Tan Hiep Phat to develop ten high-speed lines at Tan Hiep Phat factories located from North to South Vietnam. These are among the earliest aseptic PET filling lines in Vietnam, recognized by FDA standards for low-acid products.
The collaboration between the two companies provides beverages that are nutrient-rich, while maintaining natural colors and flavors without preservatives. Additionally, this technology helps the company reduce plastic use in the production process by minimizing bottle weight, decreasing production losses, and conserving electricity and water.
In the coming time, GEA will work with Tan Hiep Phat on several projects based on the GEA ECOSpin2 ZERO aseptic filling cluster and GEA Modulbloc technology. The focus will remain on developing equipment to achieve the "GEA Add Better" label, which signifies enhanced sustainability practices. The primary goal is to minimize plastic usage as much as possible. Aseptic filling technology will also ensure reduced plastic use while enhancing sensory qualities and extending the expiration date, thus enabling broader consumer reach in a more sustainable manner.
![]() |
Cold aseptic filling technology line supplied and operated by GEA at Tan Hiep Phat's factories |
In addition, GEA is introducing several technological innovations for other equipment in the production line, such as bottle blowing machines. Besides current bottle blowing technology, GEA has developed aseptic blowing technology, which also contributes to reducing plastic use while significantly saving water and energy. These elements will play a crucial role in achieving the Net Zero target by 2030.
![]() | Joining forces with the world's leading partners, Tan Hiep Phat improves recycling and green production capacity Husky Technologies, the industry’s leading technology provider of plastic injection molding solutions, has worked with Tan Hiep Phat since 1993 to provide high-end technology to ... |
![]() | Tan Hiep Phat and its 3-decade Journey of Business Development, Building Sustainable Values for Society Tan Hiep Phat Company, with its extensive network of factories spanning from North to South, is dedicated not only to globalizing Vietnamese brands but also ... |
Recommended
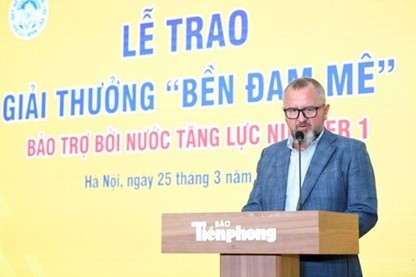
Number One Affirms Energetic Spirit at "Enduring Passion" Award
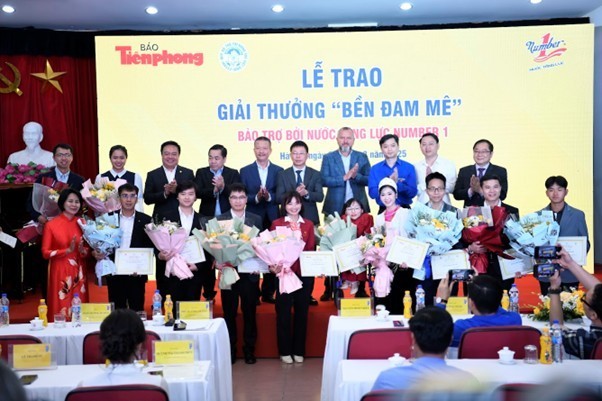
"Enduring Passion" Award Spreads Spirit of Perseverance and Dedication to Vietnam Youth
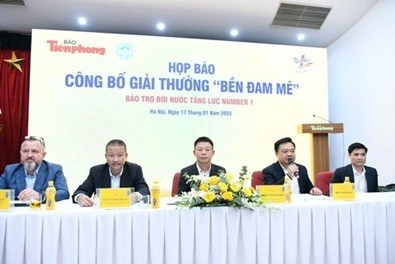
“Enduring Passion” Award Review Process to be Completed by March 25
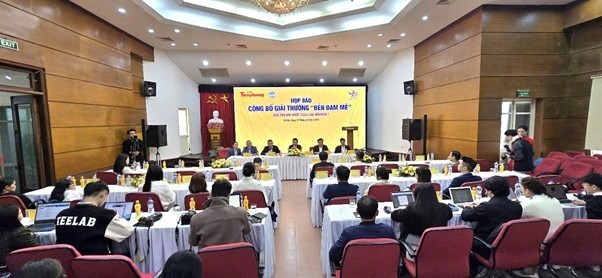
"Ben Dam Me" Award: Encouragement from Number One
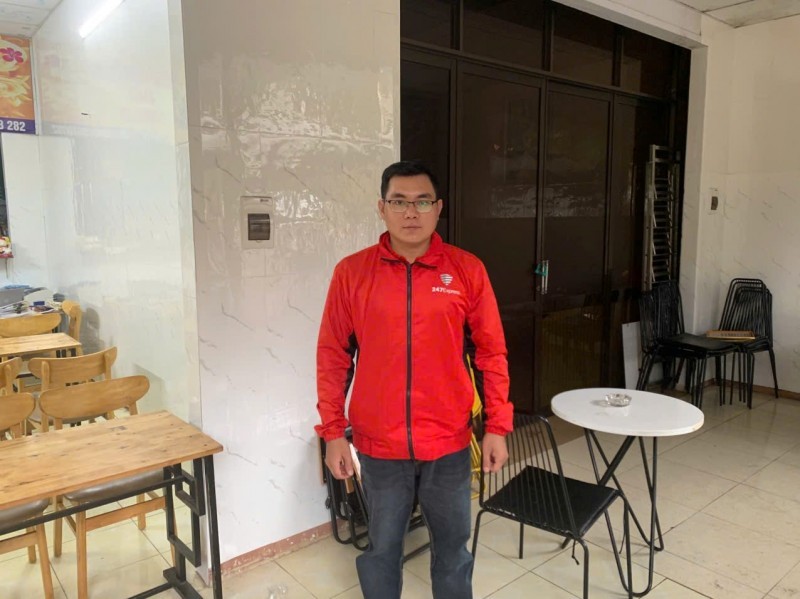
Drinking Zero Degree Green Tea, a Delivery Worker Wins VND 250 Million during Tet
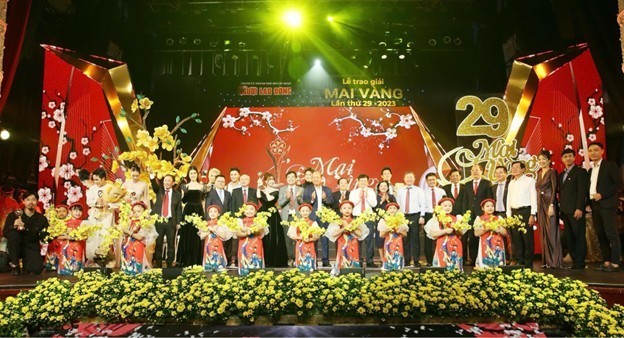
What to Expect at 30th Mai Vang Awards in 2024?
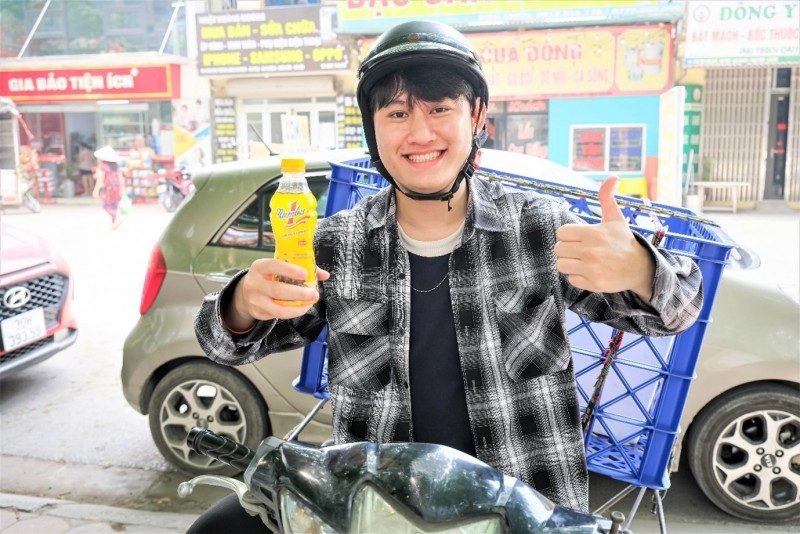
Boost Your Productivity: Tips for a Productive End-of-Year
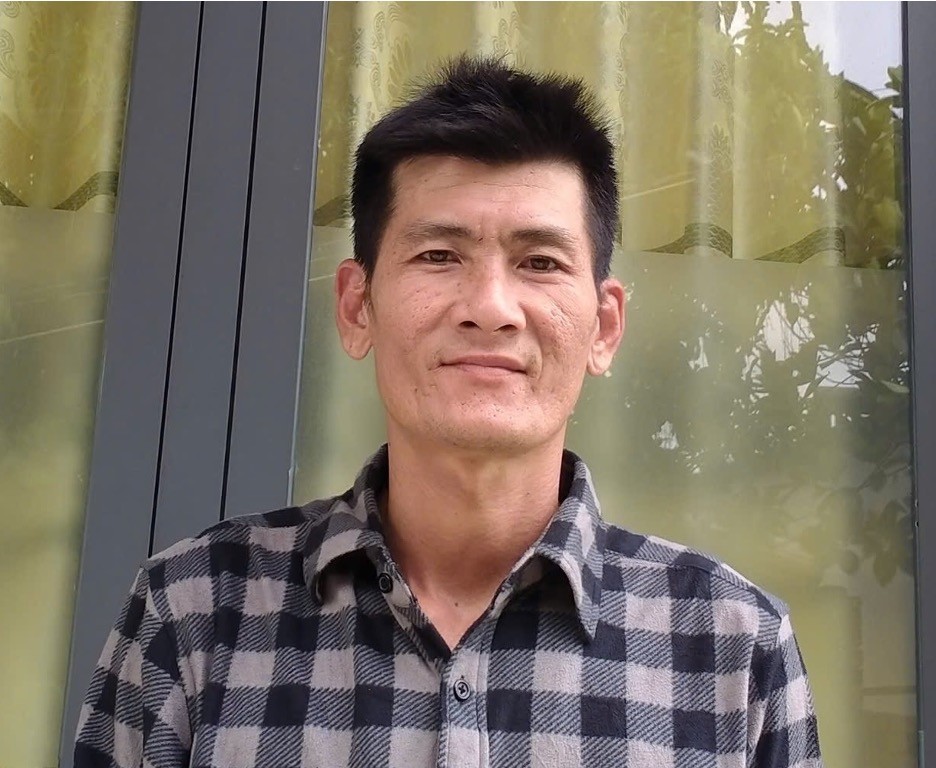