Weekend getaway in Phu Lang ceramic village
(VNF) - Leaving behind crowded streets, skycrapers in the bustling and hustling city, we decided to spend our weekend in a small village located 60 km away from Hanoi. The village, lying alongside the poetic Cau river, amazed us at the first sight by its unique charms.
In Phu Lang (Que Vo commune, Bac Ninh province), narrow zigzag lanes, red brick walls and green bamboo hedge - exotic features of a Vietnamese old village in folk tales seem to remain unchanged.
The scenery, which is hard to find in Vietnamese countryside nowadays, definitely matches with the quintessence of traditional culture which keeps being treasured here for centuries.
Walking around the village, we were impressed by the image of ceramic jars, vases and pot lining on the road side. These items, without speaking a word, showed us all about the well-preserved traditional work of the locality: ceramic ware making.
Phu Lang pottery village was founded and flourished during the Tran Dynasty (13-14th century). Today, several potteries dated back to the ancient days are still preserved and displayed at the Vietnam History Museum.
Phu Lang today, like a flower quietly spreads its fragrance, is an appealing destination for both Vietnamese and overseas visitors by its unique charm.
Ceramic picture, exotic art work of Phu Lang which embodies both traditional and modern beauty
While ceramic in the former Tho Ha ceramic village (Bac Giang province) were made from green clay, Bat Trang ceramic is of white clay, Phu Lang ceramic is made of red clay.
Phu Lang pottery products are quite varied, ranging from intricately carved devotional items like Buddha statues, incense burning box, urns, ceramic pictures, to simple household utensils like jars, vases, decorative tiles.
Decorative patterns on ceramic products are also varied, featuring authentic symbols of Vietnamese traditional culture like lotus, old temple, paddy field, or people in farming activities like ploughing, fishing, harvesting fruits.
Today, the patterns are highly persified with other images such as the country's iconic sights such as Ha Long Bay, Hoan Kiem lake, Turtle Tower or charming young lady in Ao dai.
With their distinctive beauty, Phu Lang ceramic and pottery now are found in various provinces and cities across Vietnam and even overseas.
Randomly stopping by a workshop in the village, we were warmly welcomed by the potters there, whose sweaty faces shined with sincere smiles.
It was almost 12 pm, and all the potters were about to take lunch break. "What a pity! We'd love to learn how vase and jars are made!"- one of my friend said. "Yes, I think we have no choice but ... coming back after an hour" another one said, not want to bother those who had been already tired after hours of working.
Fortunately, upon knowing our plan of leaving, the potters, who were extremely hospitable, did not hesitate to arrange some seats for us to spend our lunchtime in the workshop.
After sitting down to grab some bites of snack and sipping some water, we started our self-guided tour around the workshop.
We took the chance to observe closely and taking pictures of objects we had never seen before. Firewood, tunnel kiln, raw clay and the spinning wheel, they were all here for the curious explorers.
We even tried to make pottery on our own. The first attempt was not successful, but at least, we learnt something.
Is it difficult to craft a cup?
As promised, the potters - whom we were eagerly waiting for, came back at 1pm. We were overjoyed to see them demonstrating their well-polished skills in crafting ceramic ware.
Do you how a tall vase was made by the professionals? To me, it somehow resembles a baking process.
The first step is selecting and processing raw materia. Just like in baking, nothing can replace the quality of flour, in making potteryware, the quality of clay must be taken into account. Most of the raw materials used to produce Phu Lang pottery ware are collected from Thong Vat, Cung Khiem (Bac Giang).
Raw clay and mixing machine
The mixture afterwards is continued to be filter pressed. The resulting clay which is thick, rather dry but glutinous, is later chopped into fine pieces, remove impurities and excessive moisture, then made into smooth and soft cylinders that are ready to be molded or formed.
The second step is shaping are all executed by hands. Normally, two workers are needed to complete this process. One is responsible for handbuilding and one is responsible for shaping and wheel throwing.
Two workers who take on the shaping work are women, one (left) is in charge of handbuilding while the other is in charge of wheel throwing
Handbuilding works generally includes slamming, pressing, kneading the clay to remove air bubbles and extra moisture, making sure it is smooth and elastic enough to be moulded. (Just imagine you're kneading dough for your homemade bread.)
After that, the clay is rolled into long rope, which later is shaped into clay ring (from the front view). You can say it looks like a brown donut, from the side view.
Layers of clay rings are prepared to be throw onto the spinning wheel
A tall vase is normally made of stack of clay coil
While the handbuilding potter is working, the other put the clay on the center of the wheel head. In old days, people had to spin the wheel using their feet, but today, this hard work is less heavy thanks to the invention of electric spinning wheel.
The artisans then will bring the clay up into a tower shape by placing both hands firmly against the spinning clay.
As the clay conical shape grows taller, the potter stack the next layer of coil, one by one on top of the previous. When merging two layers, they have to make sure that one hand is supporting the clay on one side while the other hand smudging the other side.
When the shaping work is finished, the vase might be painted or carved, engraved given decorative details like flowers and leaves before entering an indispensible step: glazing.
Glazing determines the color, glossiness and firmness of the product. A special feature about made-in-Phu Lang ceramic ware is the home-made glaze which has the texture and color of natural honey. The glaze is made from special trees ashes, mud, grinded pebble and quicklime lump in a secret recipe.
After the glaze is applied, the product will be dried under the sun.
This step usually takes 1 - 3 days to complete, depending on weather condition and the size of the ceramic ware.
Vases being dried under sunlight
Last but not least, it is firing.
Fuel for firing are around 20-meter long wood chopped into proper size, stacked, and ensured to be as dry as possible before the firings of the kilns begin. Most of the source of heat are eucalyptus wood from nearby provinces like Tuyen Quang and Thai Nguyen.
Stack of wood waiting to be dried
Pots are baked in giant brick kilns at initial temperatures of 600oC rising gradually to around 1,200oC.
The temperature must be watched closely to make adjustment if necessary, as it is critical to the success of ceramic production.
Source of heat - dried wood lying readily around the tunnel kiln
Here it is, our finished product
And here it is, a lovely vase, as fresh as hot bread taken out of baking oven. The trademark coat of thick eelskin enamel that gives the brown clay an original yellow tint is what we can see in most of Phu Lang ceramic products.
The products afterwards will be carefully examined in terms of quality before being stored in warehouse or transported to selling points.
Actually, we were searching for something to buy small cup, vase or bowl as souvernirs during our trip to Phu Lang, however most of the products here are in large size, or to be distributed in bulk to retailing shops or exported.
Nevertheless, we left empty handed, but our hearts were fulfilled with fresh experience, new understanding about motherland's precious culture and the kindness of people./.
( Phi Yen )
Recommended
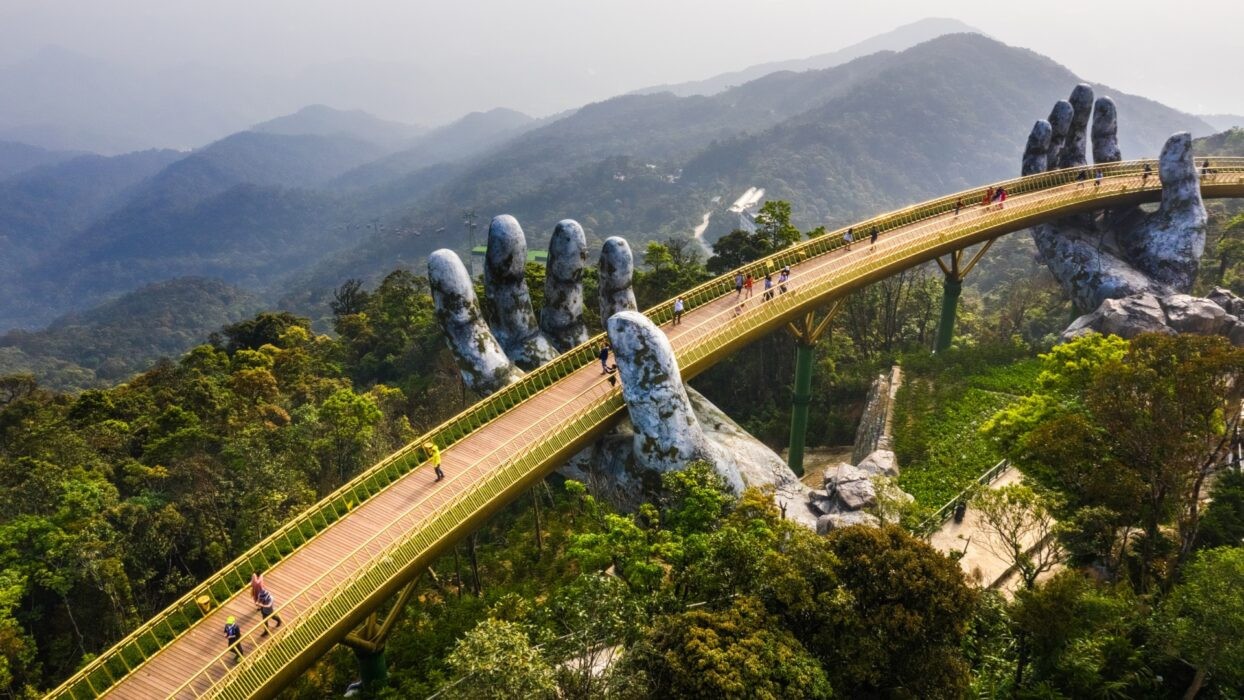
Vietnam Strengthens Its Presence On The Global Tourism Map
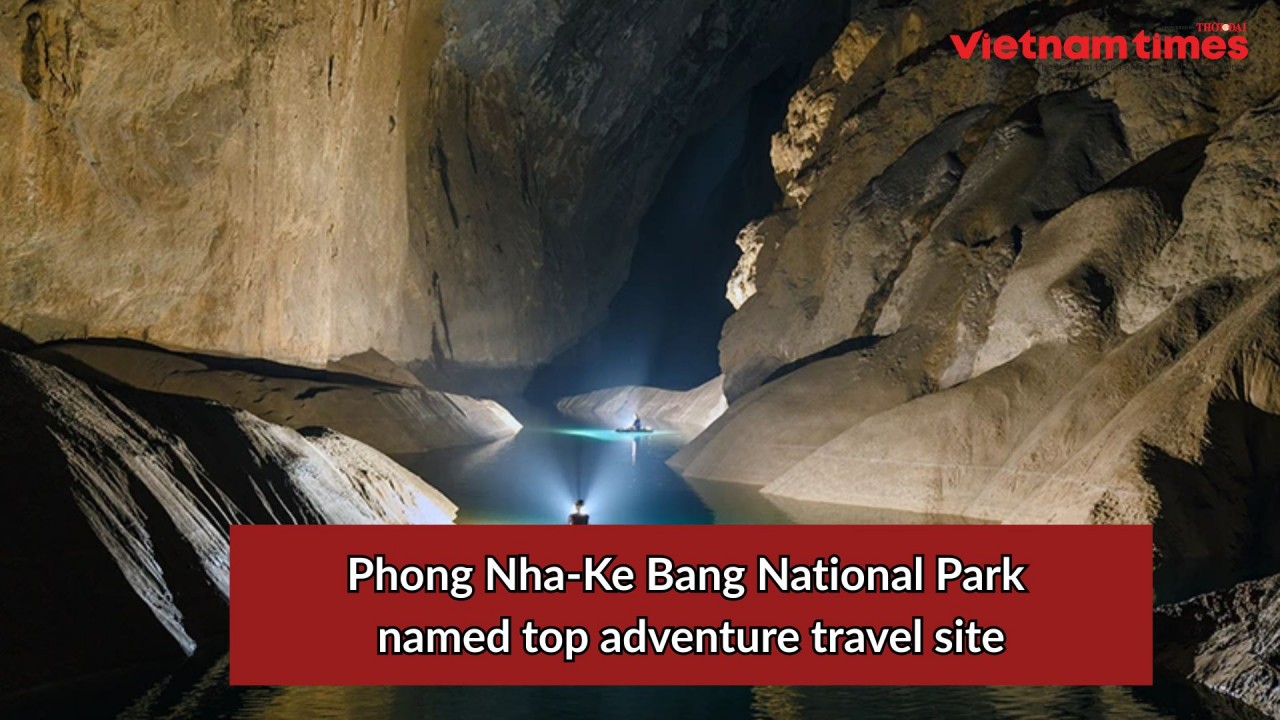
Phong Nha-Ke Bang National Park Named Top Adventure Travel Site
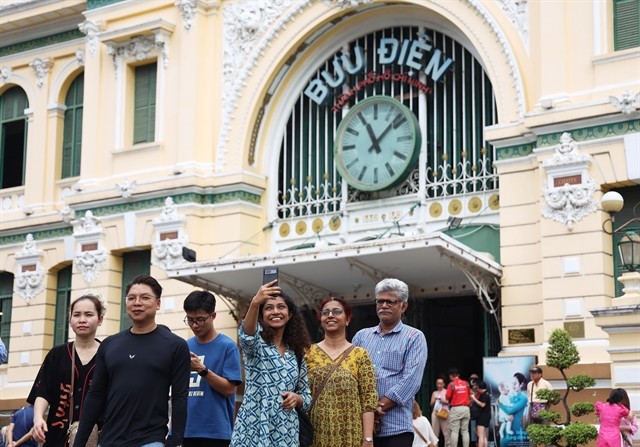
Vietnam Welcomes Record-High Number of International Visitors
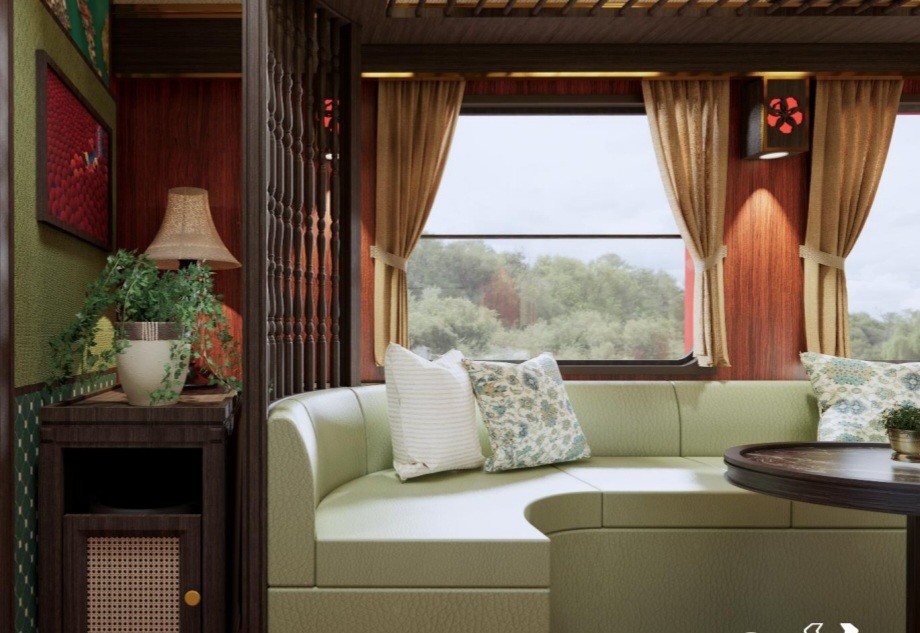
Luxury Train From Hanoi To Hai Phong To Be Launched In May
Popular article
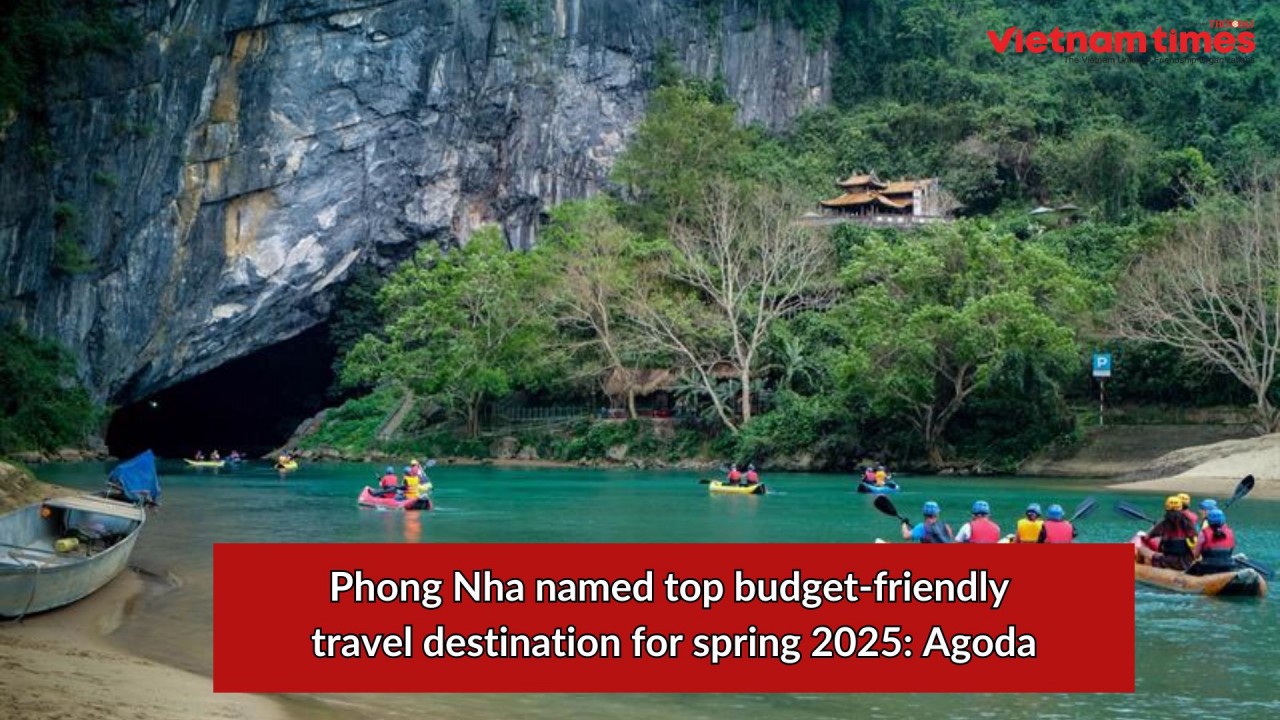
Phong Nha Named Top Budget-Friendly Travel Destination for Spring 2025: Agoda
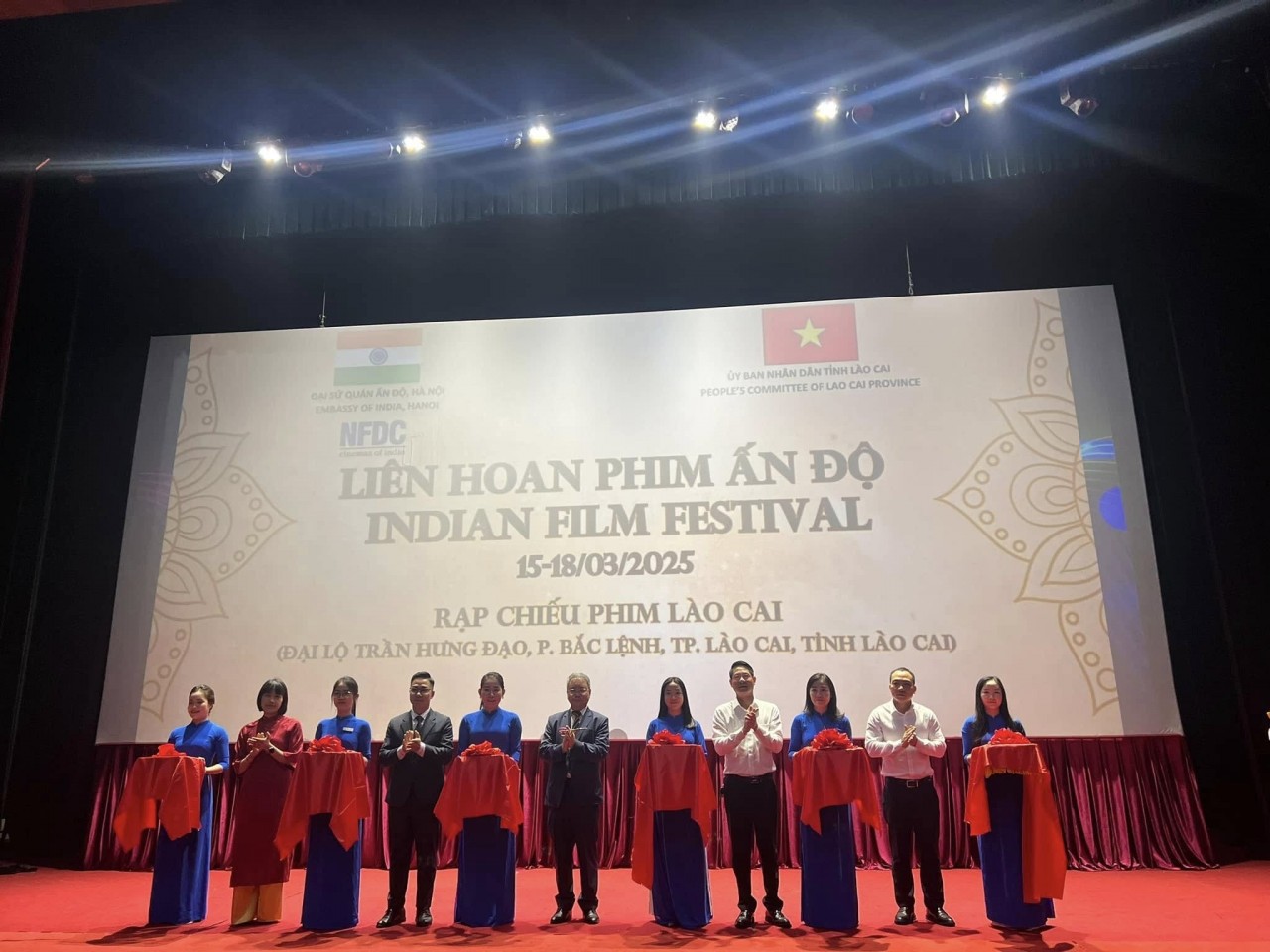
Four Indian Films Introduced to Lao Cai Audience
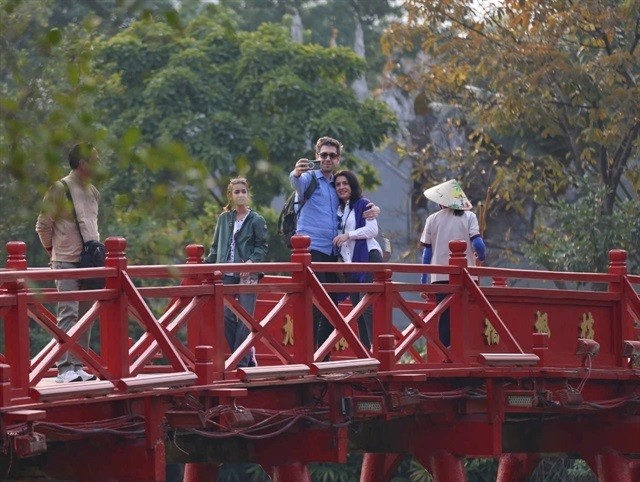
Vietnam to Waive Visas for Citizens from 12 Countries until 2028
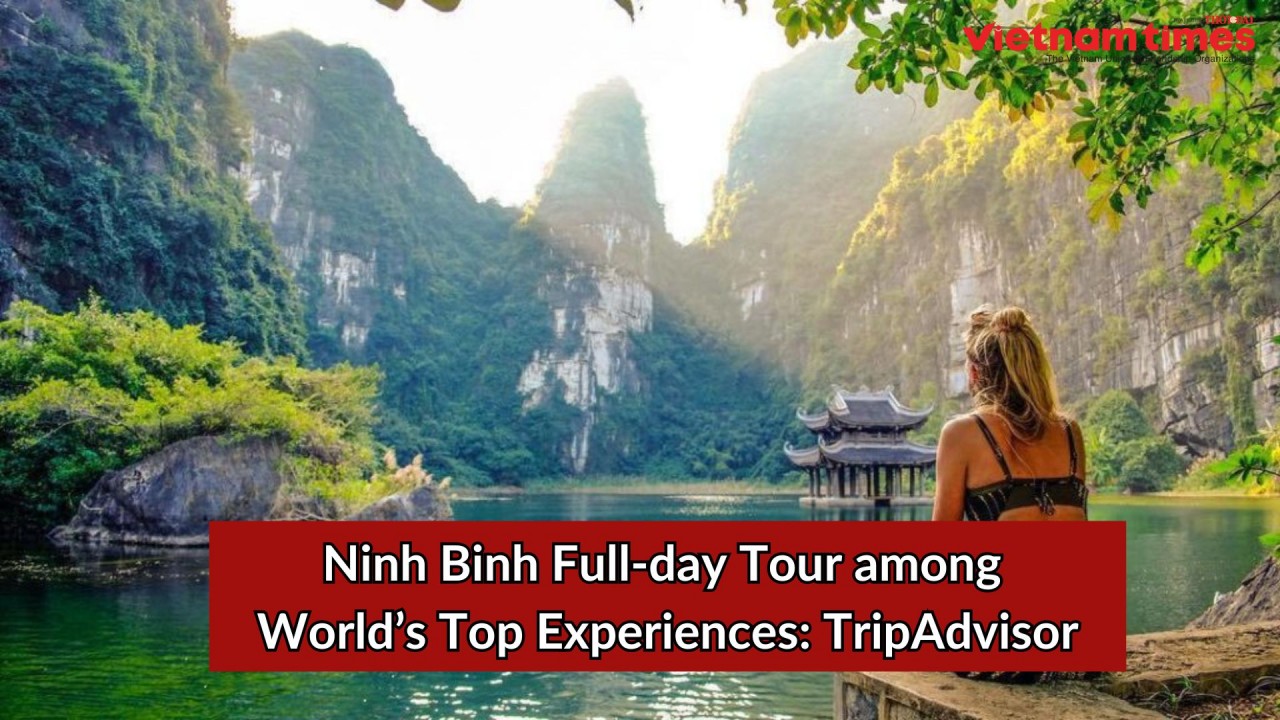